Polyurethane & Silicone Caulk: Which is right for your project?
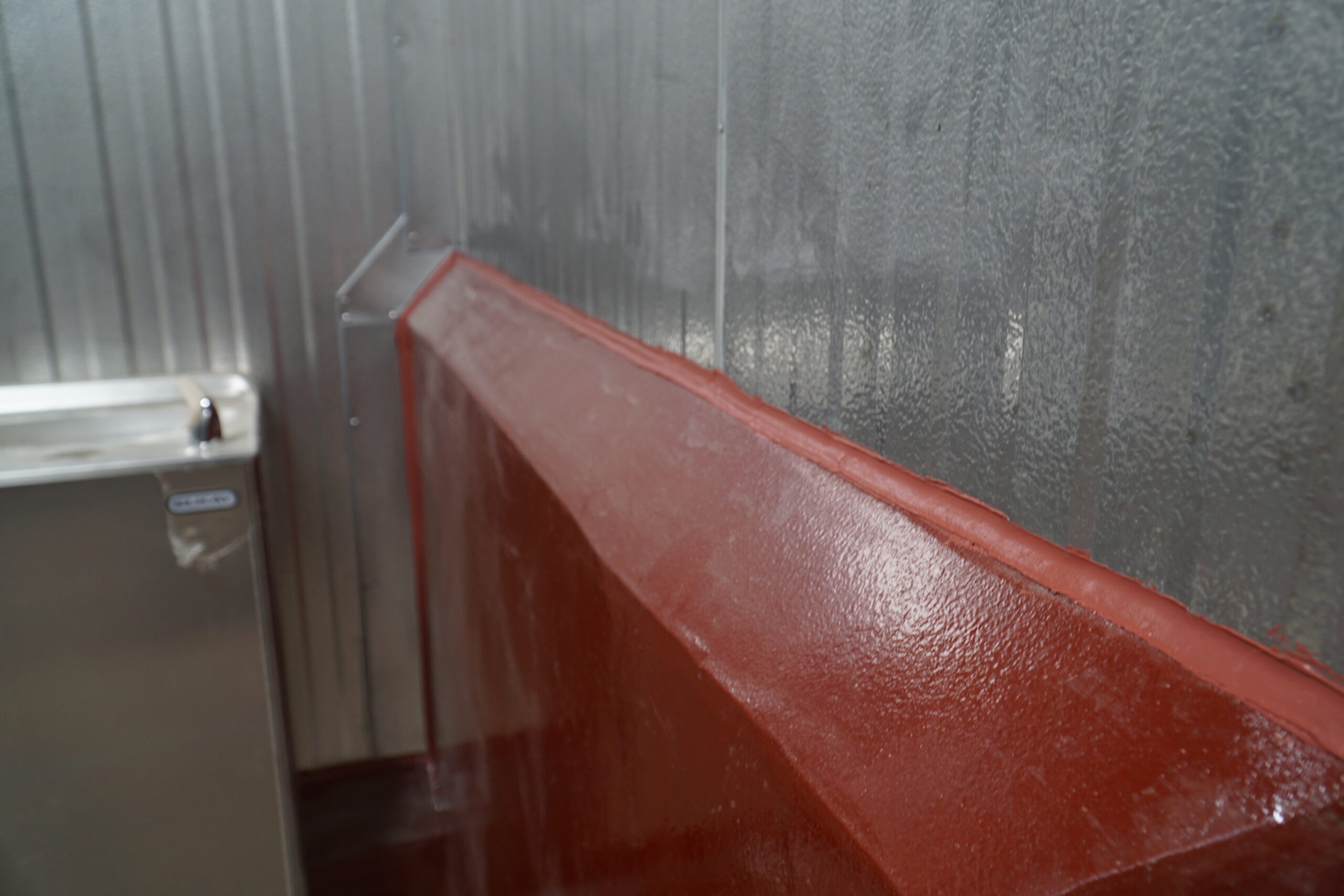
What is the difference, and why does it matter?
When it comes to your commercial property, choosing the right sealant, commonly called caulk, can make all the difference. While sealant on its own is not a particularly expensive service item on your building, choosing the wrong type can result in basically throwing your money out of the window. Each has its own unique set of properties, uses, and requirements. Let’s dive in and explore the differences.
Polyurethane
Commonly referred to as simply ‘urethane,’ this is the standard sealant in new-build and renovation commercial construction. Urethane sealants are available in both single-component and multi-component formulas, as well as self-leveling, semi-self-leveling, and non-sag formulations. The curing mechanism varies depending on the product and falls into a chemical-cure and moisture-cure category.
Urethane is the most cost-efficient choice, usually running between 60% and 75% of the material cost of silicone, depending on the specific product.
Other advantages include:
- Adhesion to a wide variety of substrates
- Ability to be used across many joint sizes
- Non-staining
- Good elastic properties (ability to stretch and recover)
- Paintable (dependent on product and paint)
- variety of colors available from factory or tint base and pigment
Some limitations to Urethane sealants include:
- Shorter service life (5-10 years)
- Primer may be required for proper adhesion
- joint movement is less than silicone
- subject to reversion (chemical bond breakdown over time)
- UV resistance is less than that of silicone
- Can get stiff in extreme cold
- Will not bond to silicone
Silicone
Silicone has seen a rapid ascension to the gold standard of design professionals and building owners alike. From the design professional aspect, the taller the building, the harder it is to service joints. Silicone has a long service life (10-20 years) and is the best sealant for bonding to metal and glass. From a building owner’s standpoint, many structural silicones carry a 20-year warranty from the manufacturer, and that brings peace of mind, though not quite as much as you would think.
Perhaps a future blog on manufacture’s warranties is due.
Silicone comes in the same variety of properties, formulations, and applications as polyurethane (e.g., sing/dbl component, self-level/non-sag, cure mechanisms, etc.), but a different set of advantages and limitations.
Some advantages include:
- A vast range of modulus formulas (ability to be stretched)
- Superior joint movement capability
- Long service life (10-20 years)
- Superior UV resistance
- Wide range of application and service temperatures
- The surface does not crack, or ‘alligator’ like urethane
- Many silicones are USDA-approved
Limitations are:
- Some silicones cause surface staining
- Silicone is not paintable, excluding silicone coatings
- Once silicone is used in a joint, you will need to replace it with silicone in future replacements
- Tendency to collect dirt and pollutants
- Higher raw cost than urethane
- Discoloration occurs when put in contact with certain substrates
- Priming is required in some applications
- In general, adhesion strength is less than that of urethane
So which should you choose?
The quick and easy answer is to replace your sealant with what is currently in place. If you have silicone in place, replace it with silicone. If polyurethane is in place, replace it with polyurethane.
The more complex answer is to ask your contractor. Qualifying your contractor is maybe the most critical step when you put your project out to bid. A knowledgeable contractor will specify the correct type of material for your project and the correct product for the given joint design and substrate. Said contractor will also be able to explain why that material is being specified.
Qualifying your contractor before awarding a contract will save you money and frustration. While their price may not be the lowest, you will be more likely to receive high-quality work performed with the correct material and design and a contractor who will stand behind their warranty. Ask your contractors questions, form working relationships with quality contractors, and educate yourself.
At J.S. Goray, we pride ourselves on being experts in our field. If you have questions about a building spec or want to double-check something your contractor quoted, we would gladly answer them, even if you are outside our service area.